What Is Cross Docking, and Why Should You Care?
27 Oct 2023
21 Min
453 Views
To reduce logistics costs and increase the amount of free capital for investing in their own development, the world's leading manufacturers and trading companies, such as Amazon, Walmart, McDonald's, Nike, C.H. Robinson, etc., have integrated cross docking technology in their flows. It is a mobile, strictly regulated, well-organized, and therefore very progressive method of processing goods.
Using a cross docking system makes it possible to minimize the costs of organizing warehouse operations by 30-35% due to the absence of a storage area. Cross-docking also allows for faster delivery of goods to the end consumer.
In this article, we will delve into the world of cross-docking, sharing the invaluable expertise of our Cleveroad company. Join us to explore the potential of cross-docking and uncover its numerous benefits to supply chain management.
What Is Cross Docking, Its Types, and When Is It Commonly Used?
Cross-docking is a set of logistics operations within the supply chain. During the cross-docking operations, shipment from the warehouse, and delivery of goods to consignees are coordinated as accurately as possible in time. It is done to eliminate the storage of goods, and acceptance of items from suppliers.
Sometimes, the cross docking process is understood as the direct transshipment of goods between vehicles or carriers. In this case, the logistics chain becomes extremely simple, and the time from ordering goods to delivery is significantly reduced.
The connotation of cross-docking differs from industry to industry:
- In the consolidated cargo transportation industry, cross-docking involves moving cargo from one vehicle directly to another, with virtually no storage.
- In retail practice, cross-docking operations can be used to concentrate goods. In this case, incoming products are sorted, consolidated, and stored until outgoing batches are shipped.
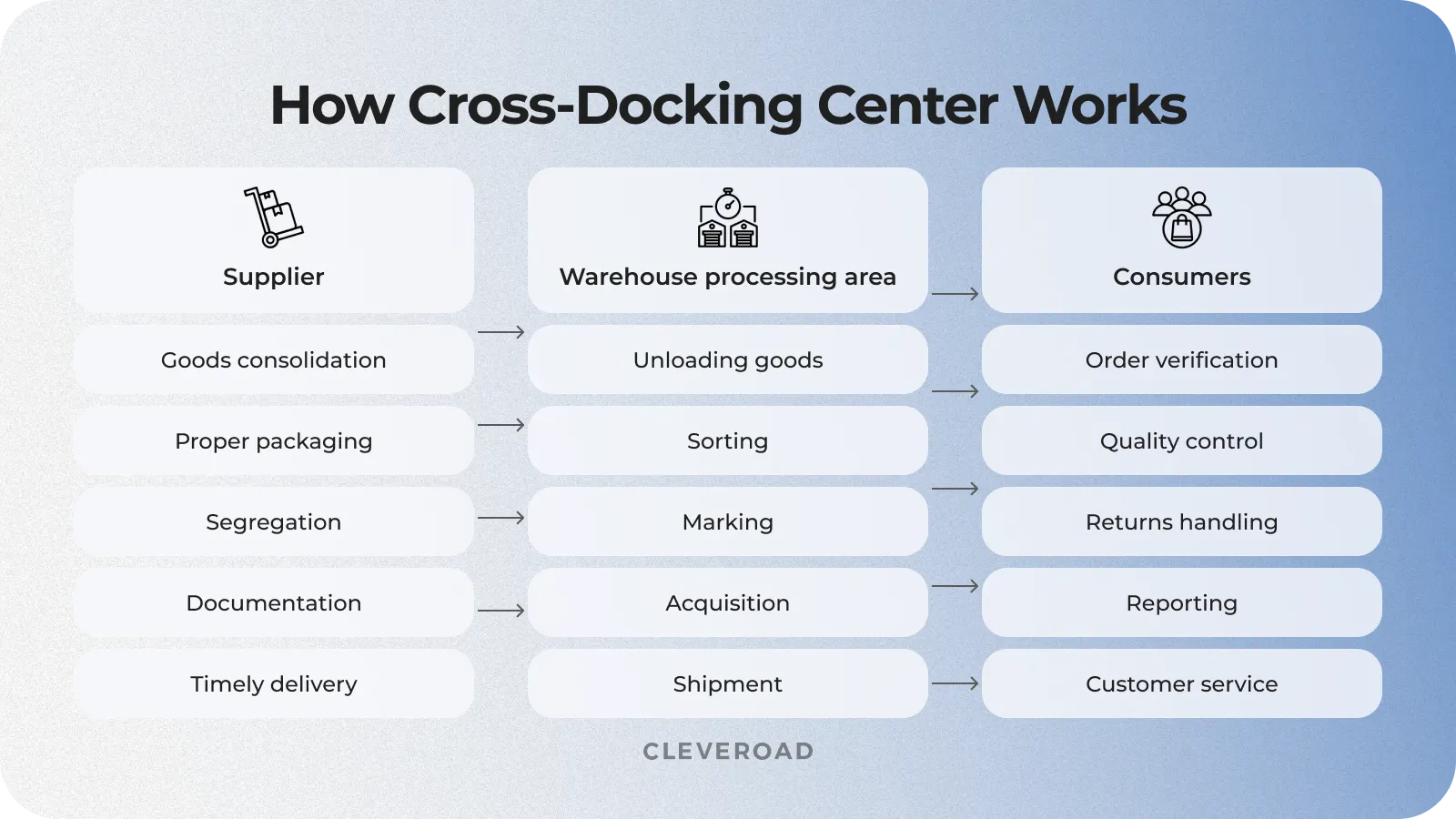
The simplest cross-docking center diagram
The necessity for cross-docking is dictated by the need to quickly speed up the process of sending and receiving a cargo of the ordered volume and packaging by the end consumer.
According to our practice, the logistics businesses apply for cross-docking software because of the following reasons:
- Repacking of warehouse space with its subsequent transportation with changed commodities, or cargo units
- Direct transshipment of cargo from a truck into a container or several smaller vehicles
- Assembling goods into sets from various shipping warehouse locations
- Direct transshipment of freight from one vehicle, with the destination in a cross-docking site, into another vehicle heading to end consumer (another warehouse/a third-party cross-docking point)
In a cross docking system it is preferable to process small batches, mixed pallets, goods characterized by high turnover and predicted demand, perishable goods (e.g., vegetables, fruits, meat), return flows. Now, let’s determine the types of cross-docking systems responsible for the above-said.
Types of cross docking to know about
Currently, many transportation organizations are shifting from traditional distribution management models to cross-docking, choosing one of the two main types of cross docking:
- Pre-distribution
- Post-distribution
Pre-distribution cross-docking. Goods are unloaded, sorted, and repackaged based on predetermined distribution instructions. If the warehouse staff knows the end customer before the supplier sends out the goods, they will promptly unload, sort, and repackage the shipment according to pre-established distribution instructions upon its arrival at the dock. Moreover, the inventory moves quickly through the cross-docking warehouse. It's best for retailers who handle their warehouses and have direct knowledge of customer and supplier relationships.
Post-distribution cross-docking. During the post-distribution process, goods are stored in the cross-docking facility until the next stage of the journey is determined, involving mapping the demand and identifying customers. This type of service would cause inventory to remain at the cross-docking warehouse for slightly longer. However, distributors and retailers can carefully consider which location to ship inventory to by analyzing inventory forecasting numbers and current inventory counts.
What and How Businesses Can Benefit from Using Cross Docking System?
Understanding how cross-docking can optimize your supply chain is crucial in manufacturing, retail, distribution, or any other industry. We will provide a comprehensive list of related businesses and the types of companies that can benefit from cross-docking solutions.
Business | Value of using cross-docking |
Food and distribution |
|
Pharmaceutical sector |
|
E-commerce |
|
Automotive companies |
|
These businesses are examples of how to use cross docking operations to make processes thrive. However, before deciding to apply cross-docking in your warehouse, it is essential to perform an internal assessment of how its use would impact overhead costs and how operations are run.
Business roles in cross-docking operations
There are various business roles in the cross-docking system. However, they can vary depending on several factors, including the specific industry, company size, and supply chain strategy. We will explore the typical business roles associated with cross-docking.
Role | Responsibilities |
Warehouse manager | Ensuring efficient goods storage and inventory management |
Cross-docking manager | Integrating cross-docking into existing supply chain workflow |
Transportation manager | Managing logistics and route optimization |
Inventory analyst | Analyzing forecasts and orders metrics |
Operations specialist | Identifying and implementing improvements for cross-docking operations |
Quality control manager | Ensuring regulatory compliance and quality standards of products |
Sales manager | Handling customer orders and communications |
IT specialist | Implementing solutions for tracking and data integration |
Overall, the variation in business roles within a cross docking definition may differ by factors like company strategy and goals, company size, type of software, specific business needs, supply chain complexity. All the enlisted specialists face different problems while working with cross-docking integration to internal company flows.
What Do Supply Chain Processes Can Be Automated with a Cross Docking System?
We’ll discuss how the cross-docking is used in different logistics processes for you to discover more.
Warehouse automation. Since the intensity of freight handling during cross-docking operations is much higher than during the procedure in a traditional warehouse, receiving real-time information and using it effectively while tracking the total number of shortages in orders, discrepancies, or damage in the acquired products is crucial.
Identified information must be immediately sent to clients so that they can quickly respond to deviations. For these purposes, it is necessary to have a warehouse management system and its integration with the ERP systems of suppliers and consignees.
Sorting goods process. Automation of product sorting through cross docking systems allows you to streamline material flows through the warehouse. Products are assembled in shipments to individual consumers as consumer orders are received. In some cases, packaging of products is also carried out.
Real-time tracking. Automating this logistics process involves receiving products from suppliers and shipping them to customers with little to no storage.
Route optimization. The company's inventory can be stored at the enterprise or nearby, and the rest – in warehouses from different parts of the country. An organization can either have their own warehouses, rent space in public warehouses, or use both options simultaneously. Thus, the design of WMS software is accompanied by a choice between your own warehouse and a public one.
Order processing automation. Faster order processing and optimized workflows result in shorter lead times, which can be a competitive advantage in industries where speed is critical.
Document management automation. This automation can significantly enhance efficiency, reduce errors, and improve collaboration across various departments and teams.
We've explored the power of cross docking technology in streamlining and optimizing critical process operations. As we move forward, we'll delve deeper into specific local regulations in logistics.
Core-Specific Modules to Integrate Into Your Cross Docking Systems
If you think out the functionality list to implement into your cross-docking solution, look through what we’ve prepared for you.
Receiving module
This module in the cross dock shipping system allows your company to manage incoming shipments efficiently. It includes features such as real-time tracking of incoming goods, automated notifications for arrivals, and barcode scanning for quick verification. The module also facilitates inspection and quality checks, enabling your staff to accurately assess the condition of received items.
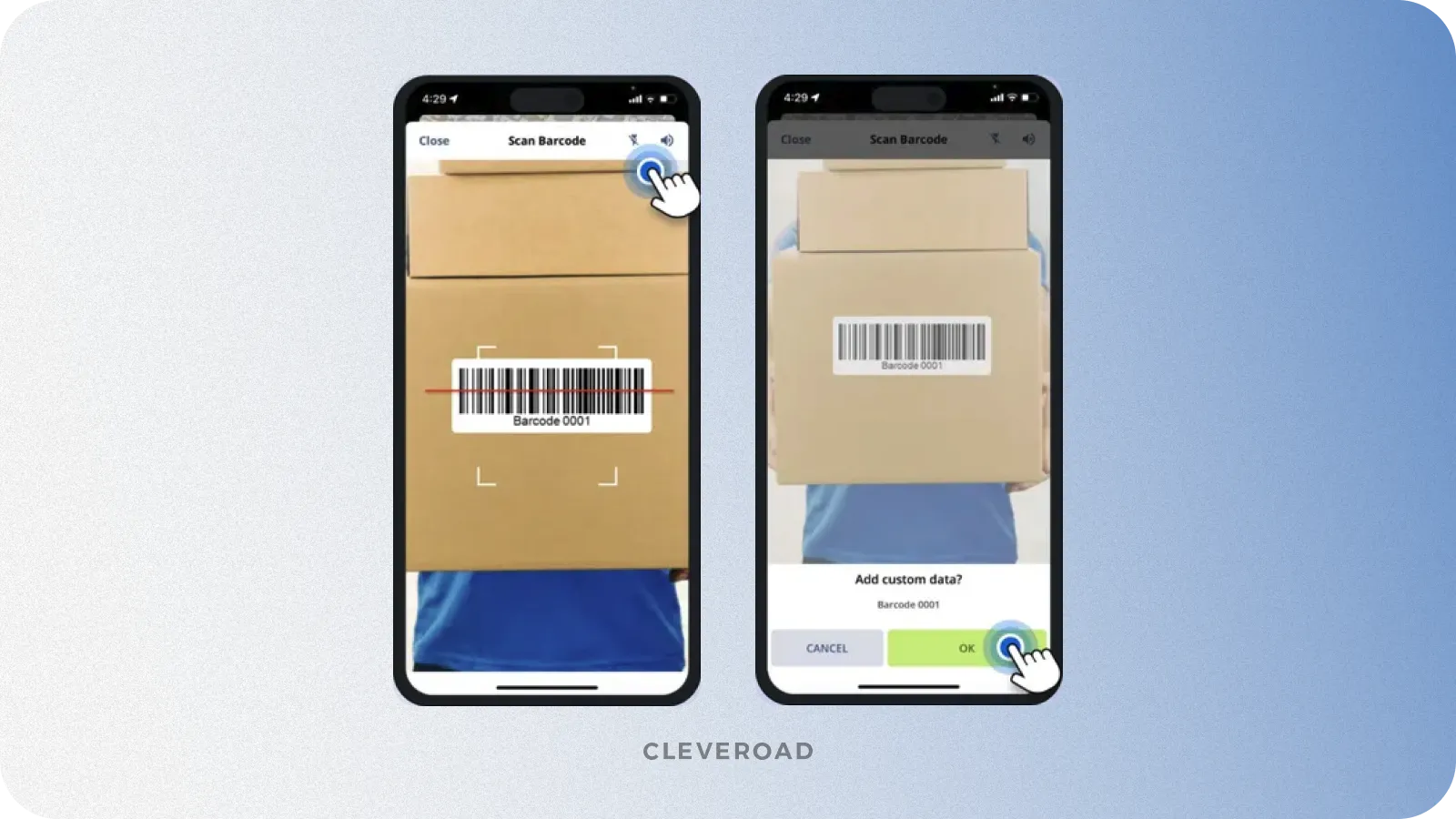
Barcode scanning example (source: Route4me)
Sorting and staging module
It organizes incoming shipments based on predefined criteria such as destination, product type, or delivery time. Moreover, the module utilizes intelligent algorithms to optimize the arrangement of items, and ensures the products are grouped logically for streamlined processing. It also includes features for bulk scanning, enabling rapid sorting and minimizing errors.
Document management
Through this feature, the cross docking system centralizes all shipment-related documents, such as invoices, packing slips, and customs paperwork, supporting digital document upload, storage, and retrieval. Additionally, the document management module enables version control and ensures that the proper documents are accessible to authorized personnel at all times, reducing the risk of errors and delays.
Loading module
This module optimizes the arrangement of products within outgoing vehicles, maximizing space utilization and ensuring safe transportation. It considers factors like weight distribution, fragility, and delivery schedules, providing loading instructions for your staff, minimizing loading time, and reducing the likelihood of damages during transit.
Moreover, you can create and use an autonomous truck load planning software in order to effectively manage loading space.
Inventory management
The module lets your company keep track of stock levels in real-time. It contains features responding for stock reconciliation, product categorization, and automatic updates of inventory levels after each transaction. Users can set up low-stock alerts and reorder notifications to prevent stockouts, ensuring continuous smooth operations.
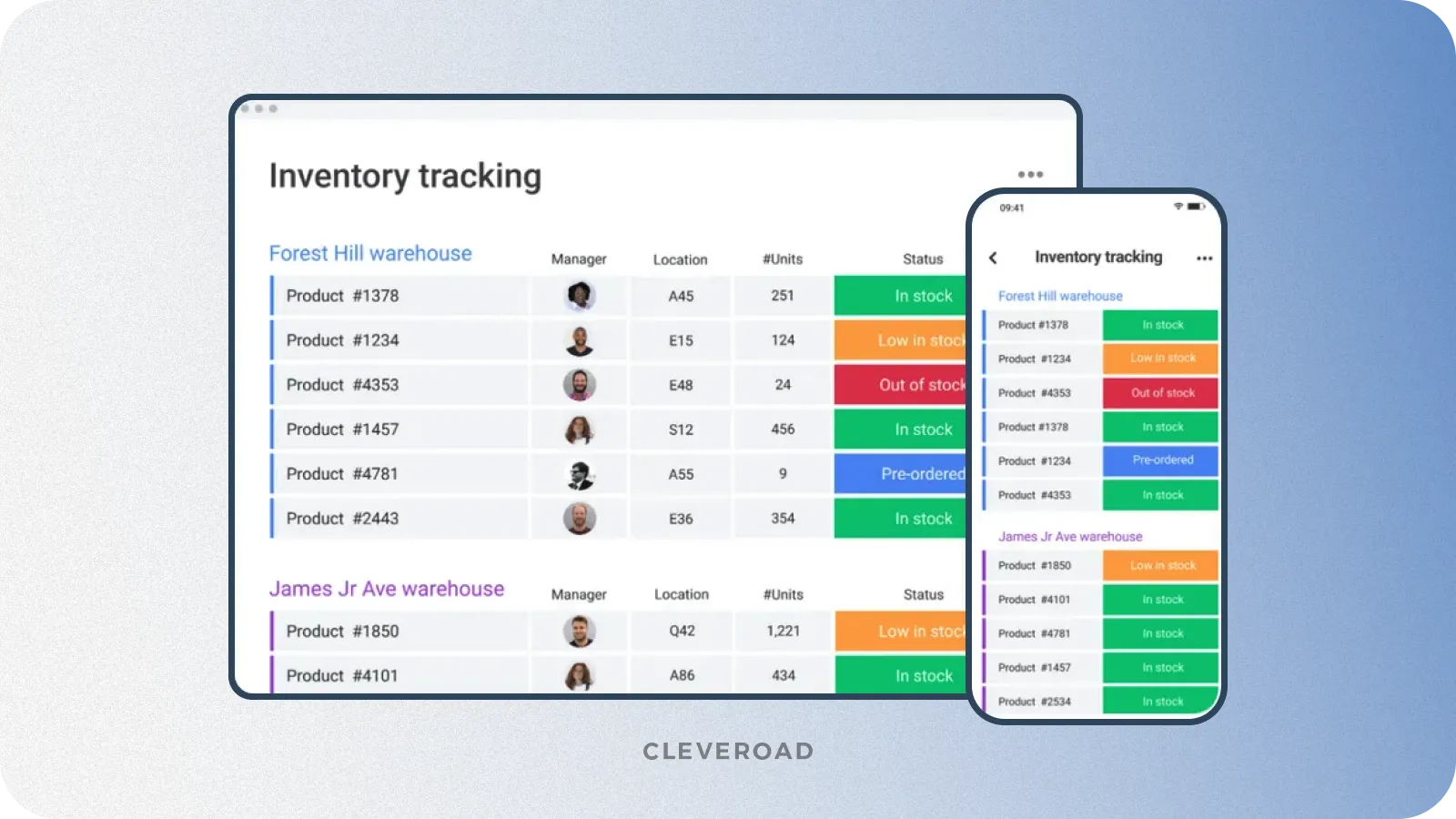
Inventory tracking feature example (source: Cloudinary)
Shipping management
The module for shipping management oversees the entire process, from order creation to final delivery. It includes features like order consolidation, address validation, and carrier selection based on cost and delivery time. This module also generates shipping labels, tracking numbers, and delivery notifications for customers, enhancing their experience and providing transparency.
Real-time analytics and reporting
Real-time analytics and reporting provide actionable insights into your cross-docking operations. It offers customizable dashboards, graphical representations, and trend analysis tools. With the help of this module, you can monitor key performance indicators (KPIs), track operational efficiency, and identify areas for improvement. Moreover, real-time analytics and reporting empower data-driven decision-making, leading to optimized processes and cost savings.
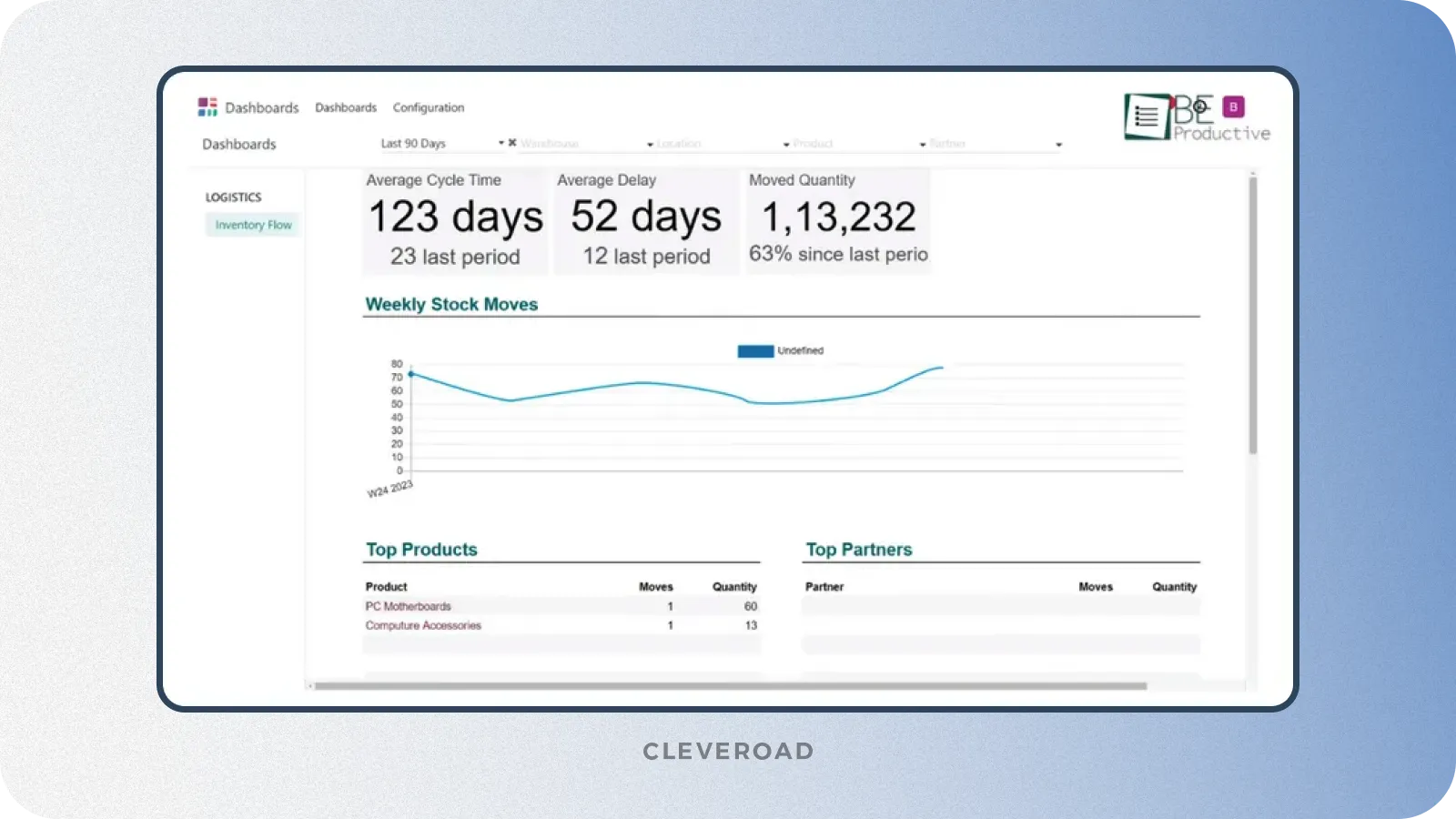
Real-time reporting feature example (source: YouTube/BeProductiveOfficial)
Integrations with other corporate systems
Integrations of your cross docking system with other corporate software enable seamless data exchange between your cross-docking software and existing business applications. This includes integrating:
- Enterprise Resource Planning (ERP) systems
- Customer Relationship Management (CRM) software
- Accounting platforms, etc.
Combining the said functionality lets your company achieve a unified view of operations, streamline workflows, and eliminate data silos, improving efficiency and collaboration across departments. However, please note that the choice of technology and specific cross docking system modules should be tailored to your organization's size, industry, and objectives.
Major Challenges of Implementing a Cross Docking System
Implementing a cross-docking system functionality can present several challenges for businesses, most notably the requirement of rapidly sorting and loading products onto outbound trucks. This can be incredibly labor-intensive if the volume of inbound and outbound shipments is too high for the available staff to manage.
Let’s discuss how to act and what to consider to properly integrate a cross-docking software into your everyday logistics business flows.
Tech requirements to facilitate cross docking process
Depending on what type of cross-docking customer needs, specific tech requirements are better suited to the logistic system than others. The list below shows some high-level tech requirements common for cross-docking implementation.
Integration with smart devices. This requirement ensures accurate tracking and timely updates on the status of each item. GPS, IoT devices, and sensors are helpful for tracking the location and status of goods in real-time.
Integration with barcode/RFID systems. Implementing Barcode/Radio-Frequency Identification (RFID) systems enables automated and error-free tracking of products within the cross-docking facility to allow seamless identification and efficient handling.
Digitizing the storing and managing shipping documents. It involves digitizing shipping documents, such as invoices, packing slips, and bills of lading. By storing and managing these documents electronically, the cross docking process becomes more streamlined.
Integrating tools to optimize transportation routes. Integrating tools for route optimization involves utilizing software solutions that analyze various factors like traffic, distance, and delivery schedules. These tools help determine the most efficient transportation routes for goods, reduce transit time, and cut operational costs. Such an integration can also be performed through a route optimization API.
Providing solutions to ensure compliance with customers. It means implementing a system that ensures adherence to customer-specific requirements. Such a system should include packaging standards, labeling regulations, and delivery schedules.
Integration with ERP system modules. This integration enhances efficiency by synchronizing inventory, orders, and financial data. To use ERP integration and discover its effectiveness, you can build ERP system from scratch along with a skilled software development vendor.
Features to generate reports for regulatory purposes. This requirement involves incorporating features within the system to create detailed and accurate reports for regulatory compliance. These reports provide essential information to regulatory authorities, ensuring the cross-docking facility complies with industry standards, safety regulations, and legal requirements.
Regulatory considerations in cross dock shipping
The requirements for warehouse activities are not often identified as separate parts of legal acts, but are indicated in the general block of requirements for business activities. However, if you start preparing for this activity adaptation, both in a professional context (e.g., commodity warehouses) and in an auxiliary context (e.g., enterprise warehouses), you will have to solve the issues of locating warehouse buildings, constructing or reconstructing warehouse buildings and premises, equipping environments, and so on.
The type of the regulation | Explanation |
Building regulations | The legislation imposes regulated requirements for the design, placement, and maintenance of all kinds of warehouses, as well as adjacent territories |
Taxation | The competent authority is exercising control over compliance with tax laws and full/timely payment of taxes |
Transportation regulations | Compliance with transportation regulations defining weight limits, vehicle size restrictions, and road use permits for trucks |
Import and export regulations | It outlines procedures for import, exports, re-export, temporary entry, and transit of goods for customs clearance, duty, excise, and other customs tariffs payments, the activity of customs brokers and customs bonded warehouses |
Weight limit | All trucks and trailer configurations have weight limits based on the vehicle’s axle configuration. Regulations stipulate the weight limitations of a truck. |
Cargo regulations | Each country has specific air cargo packaging, security, and customs requirements. Freight forwarders often have expertise in each region and ensure compliance with the regulations |
Safety standards | To ensure that movements are carried out safely, logistics must actively work on three key elements: movement planning, vehicle safety, driver and team’s competence |
Companies moving freight anywhere in the world must adhere to the latest regulations set by the governing regulatory organization, and it is essential to keep current with the latest legislation. To ensure your cross docking delivery operations are adherent to the legislation of your country, you can find a skilled logistics software development vendor who will help you with this.
For example, Cleveroad developers are experienced in creating logistics solutions compliant with local and international industry standards and regulations.
Proven Practices for Implementing Cross Docking System into Your Company
Let’s talk more about how to properly integrate a cross-docking system into your internal supply chain business processes.
Assess your company's needs
Starting cross dock system creation planning, you should first discover your business needs and determine the purposes of the system’s implementation. You can also work on your logistics software creation along with the IT development vendor. They’ll help you to conduct business researches as well as to set an appropriate feature set to satisfy your business requirements.
Additionally, weighing out your business requirements before cross-docking software development, you should consider the following warehouse design tactics:
- Warehouse shape. Long-term parameters, including product turnover, distance, gates, buffer spacing, and freight movement patterns determine the best design for each cross-docking warehouse (e.g., l-shape, rectangle, t-shape, etc.).
- Dock doors number and placement. A more efficient layout would involve doors on a single wall or at a 90-degree angle to each other, enabling fast movement between incoming and outgoing doors for high-speed mowers.
- Unbound and outbound transportation schedule. When designing and organizing a cross-dock facility (integrated with your smart warehouse management system), it is essential to take into account factors such as truckloads, transit times, and vehicle wait times.
Decide on ready-made vs.custom cross docking system
Choosing a ready-made solution for logistics, instead of the implementation of a custom system, can be applicable in some scenarios. Here are several popular ready-made solutions you can use for the cross-docking logistic process automation:
- LogiNext Mile
- CargoSnap
- Logi-Sys
- Dropon
Each of the software platforms above has its own pros and pros. However, kindly note that the ready-made solutions are appropriate if your business needs are strictly defined. In case your company scales, the ready-made logistics software may occur rigid to satisfy your growing business needs, but the custom cross-docking system will easily meet them and scale as you require.
So, this is the reason to apply to a software development vendor with expertise in logistics solutions creation, and order a custom cross docking system, easily adjusted to the requirements of your company and allowing your business to scale seamlessly.
Find a reliable logistics IT partner
Collaborating with the right software development vendor who deeply understands the cross dock meaning is crucial for the success of your project. Here's a list of the top 5 pieces of advice to consider while seeking for a logistics software development partner:
- Expertise. Look for a partner with a proven track record in developing cross-docking solutions. Check their portfolio to see if they have experience in similar projects. The more experience they have, the better they can understand your specific needs.
- Technology stack. Ensure the partner is proficient in the latest technologies and tools relevant to cross-docking software development. They should be adept at using modern programming languages, frameworks, and tools that can enhance the efficiency and scalability of your software.
- Client references and reviews. Reach out to their previous clients or read online reviews and testimonials (e.g., on professional websites like Clutch). This will give you insights into their working style, reliability, and how satisfied their clients are with their services. Talking directly to previous clients can provide invaluable information.
- Communication and collaboration. Choose a partner that is responsive, communicates clearly, and understands your requirements thoroughly. Collaboration tools, time zone compatibility, and language proficiency are also essential factors to consider, especially if you are working across different regions.
- Scalability and support. Your cross dock system needs might evolve, so ensure that the partner can scale their team and resources accordingly. Additionally, inquire about their post-launch support and maintenance services. A good partner can provide ongoing support to fix bugs, implement updates, and address any issues arising after the software is deployed.
Looking for such a partner, you can use the following options:
- Gathering in-house cross docking solution development team from the local IT experts.
- Applying to freelancers – independent specialists to create your cross-dock software.
- Outsourcing your digital product for cross dock delivery to skilled logistics software experts. Compared to the previous options, this one is much more cost-effective and reliable. Moreover, you may hand over all the necessary work to the specialists freeing up your time for other necessary logistics and transportation tasks, and only control the work of the outsourcing partner.
Read in detail on how to outsource your software development and succeed
Choose a proper solution architecture
Let's explore the key components and principles of a well-designed cross docking system architecture to ensure the seamless flow of products from suppliers to consumers. Here's an example of cross-docking project architecture that the Cleveroad team have created for its client, after analyzing their requirements.
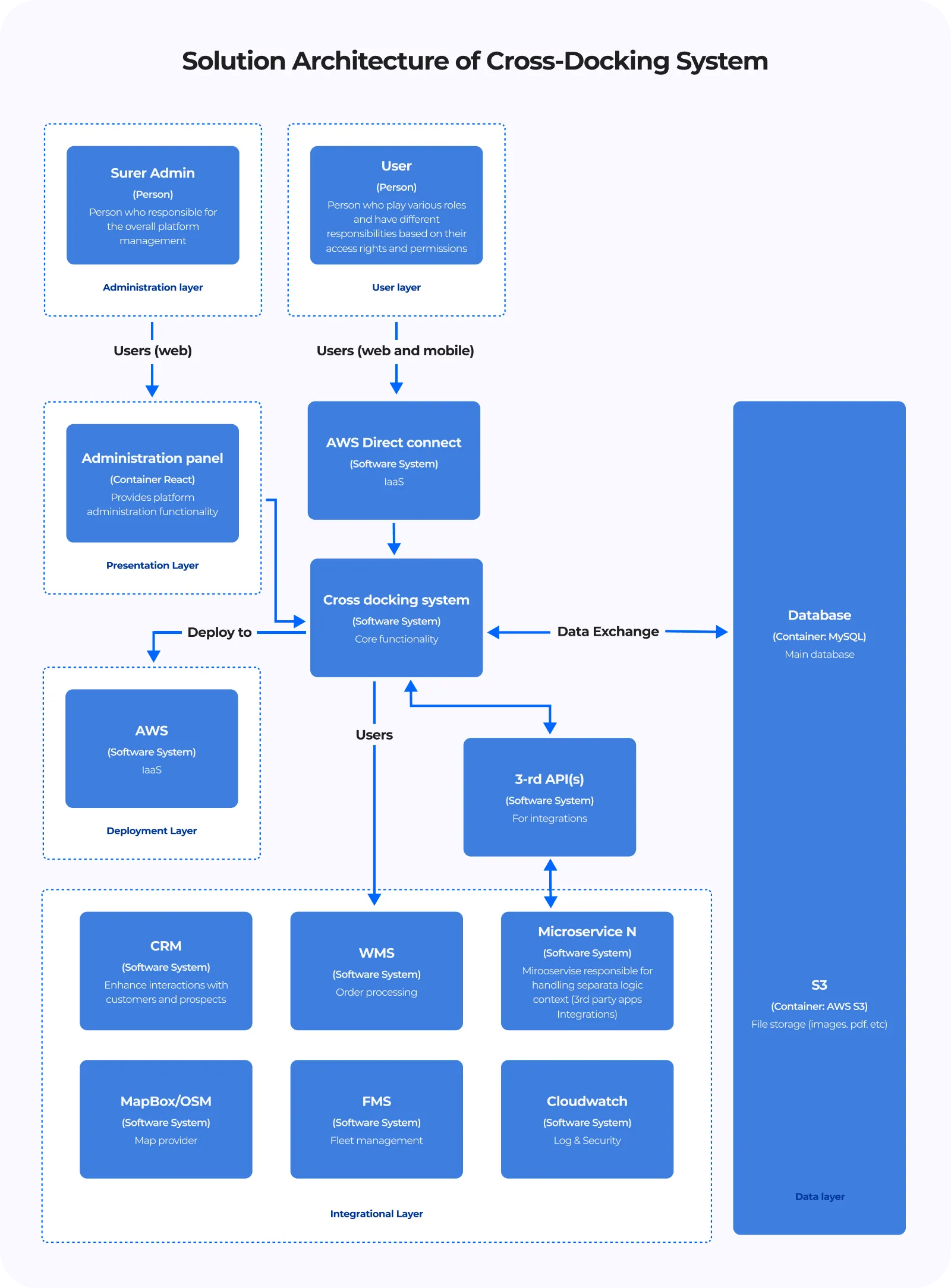
The example of the cross-docking system’s architecture created by Cleveroad
Before starting working on a system architecture diagram it’s important to gather all relevant information from customers about their needs, tech and non-tech requirements, current infrastructure and systems, current business processes and all expectations for scalability and security. Each component plays a distinct role in the overall architecture.
Deployment, integration, and support
The vendor’s team helps you not only create, but also deploy the built cross-docking system in your business environment. They also integrate it with other of your existing logistics and transportation systems (e.g., CRM, ERP, TMS, etc.).
As the cross-docking system is quite complex, you may need support and maintenance services. It means the vendor’s specialists will monitor your cross dock system, updating it with advanced features or fixing bugs.
Maksym Nazarukha
Middle business analyst at Cleveroad
“The implementation of cross-docking should begin with a pilot project. This will allow us to study the impact of this technology on a small scale and correct any shortcomings before they affect an entire product line or warehouse network. Not all the products planned for the project will necessarily be processed through cross-docking: it may be necessary to store some of it in a warehouse."
Tracking the system’s performance with the set KPIs
Let’s discuss this support stage activity of the vendor in detail. Tracking the performance of a created cross-docking system involves monitoring Key Performance Indicators (KPIs) to ensure it operates efficiently. Together with your vendor, you should establish specific KPIs such as order processing time, inventory turnover rate, error rates, and customer satisfaction. Clear KPIs provide benchmarks for performance evaluation.
Reveal more peculiarities of Cleveroad software development process with our guide!
Real-life Success Stories of Manufacturers That Adopted Cross Docking Systems
It’s high time to discuss on the examples of famous logistics companies what achievements transportation businesses gain when integrating cross docking delivery into everyday business flows.
Deere & Company
Deere & Company makes machinery for agriculture, construction, and forestry, as well as engines and lawn care equipment. They wanted to reduce supply chain costs by 10% in four years, so they changed their inventory replenishment process. They also implemented strategies such as consolidating shipments, utilizing break-bulk terminals, and contracting third-party logistics providers to optimize their network and improve efficiency, and put those strategies into life through the cross-docking software.
Due to cross docking system use, they achieved cost-management results in their supply chain, including a $1 billion decrease in inventory, a notable decrease in customer delivery lead times (from ten days to five or less), and approximately 5% annual savings in transportation costs.
Privalia
Privalia is an online fashion outlet with a large customer base in Spain, Italy, Mexico, and Brazil, totaling over 28 million. The store carries a wide range of clothing, household items, sports equipment, and products for children. The company is recognized for integrating technology into all of its production processes, that's why their example showcases the efficiency of cross-docking in action.
Privalia utilizes cross-docking at its logistics center in Barcelona, Spain to enhance order fulfillment speed. Cross dock shipping is fully utilized in Privalia operations to support flash sales, rebates, and promotions, which is commonly practiced in outlets and retail stores.
Eroski
Grupo Eroski implemented the cross-docking formula in its distribution center in Álava, Spain with the assistance of Mecalux specialists. The food sector has tight delivery deadlines as it transports perishable products. In addition, Grupo Eroski has been challenged to meet the increasing demands of customers who expect excellent service in the company's supermarket chain.
Cross-docking plays a crucial role in Grupo Eroski's logistics complex. The dedicated area for this task spans 1.48 acres and efficiently handles a large volume of orders. Using this method of the cross docking delivery, 80% of the goods are successfully sent out for same-day delivery to high-activity centers, with the remaining 20% delivered the following day.
Rough Estimation of Building and Integrating Cross Docking System: Cleveroad Example
Here, we will explore realistic project estimates, setting achievable timelines, and building the right team for success. Accurate estimations and timelines are the cornerstone of project management, helping us to plan effectively and deliver on expectations. Additionally, assembling a skilled and diverse team ensures that we have the expertise needed to bring our logistics system to life.
First, let’s take a look at the approximate time to build a cross-docking system for basic features.
Features | Approx development time (d) |
Receiving module | 146 |
Sorting and staging module | 185 |
Inventory management | 146 |
Document management | 95 |
Loading module | 99 |
Shipping management | 74 |
Automated scheduling | 110 |
Route optimization | 205 |
Real time analytics | 151 |
Real time reporting | 141 |
Integrations with other business systems (CRM, ERP) | 190 |
Total development time | 1542 |
Please consider that the above estimation is based only on the core cross-docking software functionality. The time estimates for the work of another specialists (e.g., project managers, solution architect, designers, business analysts, etc.). Their work time is estimated separately. If you require a more accurate cross docking software quote, you can contact us, and we’ll eagerly help you.
The approximate software development team structure you may need to develop cross-docking system will be:
- The solution architect
- UI/UX designers
- DevOps engineers
- Developers (front-end/backend/mobile)
- QA engineers
- Business analysts
- Project managers
As part of a project plan, a timeline concisely represents the steps required to complete each piece of work. It shows the project duration in days, weeks, months (sometimes even years) to give you a high-level understanding of your vendor’s time to complete the project.
The stages our company passes to deliver robust cross-docking software for you are the following:
- First contact. You submit the application on our website, revealing the essence of the cross-docking system you want to create.
- Solution design. Our specialists (e.g., solution architect, business analysts, and designers) work together to define the scope, create a cross-docking feature list, and design a solution that aligns with your goals and constraints.
- Discovery stage. During rendering the Discovery Stage Services, we outline your business procedures and the criteria previously gathered for your cross docking system, including the platforms you want to support, the features you want to have, the third-party services you want to connect (like Stripe or Google Maps, Shiptify, SAP ERP), and much more.
- Development and QA. Our development team works on creating the pre-defined functionality by sprints. The QA engineers check every piece of code developed to ensure the flawless work of your future cross-docking system.
- Product release. Our team helps you deploy and implement the cross-docking software in your business workflows.
- Support. Our experts keep working with your cross dock delivery software tech support if needed.
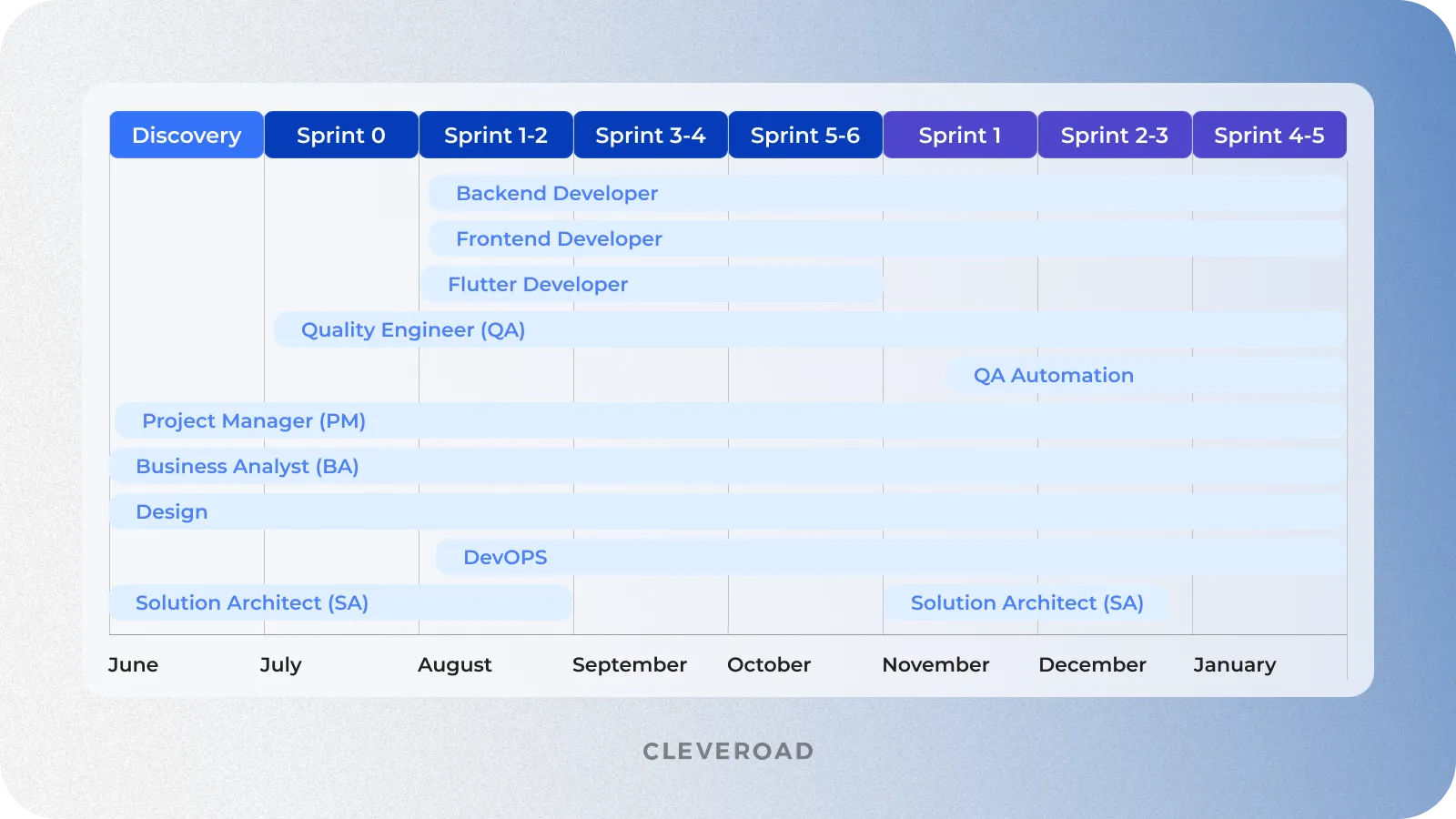
Example of the vendor timeline required to complete the cross-docking project
While estimating your cross-docking system, the specialists also evaluate possible risks the development may face. Assessment of potential risks can be broken down into three stages:
- Predicting the events or conditions that may occur in the course of cross dock system delivery
- The likelihood of their occurrence
- The impact they may have on your project
Cleveroad — Your Reliable Partner in Logistics Digitalization
Cleveroad is an outsourcing software development company with hands-on experience in logistics and supply chain solution creation. Our team develops custom complex systems for logistics and transportation businesses to enhance workflow performance and improve collaboration between shipping organizations, partners, and customers.
What are the potential benefits of collaborating with us?
- We excel in creating logistics software for transportation, fleet management, enterprise resource planning, asset management, last mile delivery, etc.
- Experience with logistics and transportation software integration, such as SAP ERP, Salesforce, Google Maps, LogistaaS, Xero, UpKeep, etc.
- We offer a thorough consultation with our domain experts to discuss the creation and integration of your software product.
- IT services on demand, include building logistics software from the ground up, integrating with IoT devices such as GPS trackers, providing software modernization services, and offering DevOps services, and more.
- Signing Non-Disclosure Agreement (NDA) per your wish in order to protect the uniqueness of your cross-docking system concept
- A variety of collaboration models available for you to choose from, such as Time & Material, Staff Augmentation, and Dedicated Team.
We want to share one of our successful logistics software development cases with you.
The company we are working with is based in the US and focuses on warehousing and long-distance cargo transportation. They required a Transportation Management System (TMS) to enhance their shipment control, streamline route planning, and improve supply chain operations. Furthermore, it was important for our client to integrate smoothly with their current business systems, specifically their warehouse management system and CRM.
Our team developed and deployed a personalized transportation management platform for the client. The solution enhanced route planning and provided the option for manual adjustments. Furthermore, a driver's application was developed to facilitate navigation along customized routes. Our team also effectively integrated the TMS with other logistics systems, ensuring the accuracy of data and preventing duplication.
As a consequence, the client got the custom transportation management system successfully, which allowed to decrease shipment losses and enhance delivery times. By utilizing a unified TMS environment, the company could effectively meet all their business requirements and subsequently increase profits.
Work with a skilled logistics IT partner
We will help you build a robust cross docking software: contact our Senior Logistics Business Development Manager to get fully consulted
Cross-docking is a set of logistics operations within the supply chain. During the cross-docking operations, shipment from the warehouse, and delivery of goods to consignees are coordinated as accurately as possible in time. It is done to eliminate the storage of goods, and acceptance of items from suppliers.
For example, in the consolidated cargo transportation industry, cross-docking involves moving cargo from one vehicle directly to another, with virtually no storage. In retail practice, cross-docking operations can be used to concentrate goods. In this case, incoming products are sorted, consolidated and stored until outgoing batches are shipped.
Cross-docking should be used for repacking of warehouse space with its subsequent transportation with changed commodities, or cargo units, direct transshipment of cargo from a truck into a container or several smaller vehicles, assembling goods into sets from various shipping warehouse locations, direct transshipment of freight from one vehicle, with the destination in a cross-docking site, into another vehicle heading to end consumer (another warehouse/a third-party cross-docking point)
Warehouse shape. Long-term parameters, including product turnover, distance, gates, buffer spacing, and freight movement patterns determine the best design for each cross-docking warehouse (e.g., l-shape, rectangle, t-shape, etc.).
Dock doors number and placement. A more efficient layout would involve doors on a single wall or at a 90-degree angle to each other, enabling fast movement between incoming and outgoing doors for high-speed mowers.
Unbound and outbound transportation schedule. When designing and organizing a cross-dock facility, it is essential to take into account factors such as truckloads, transit times, and vehicle wait times.
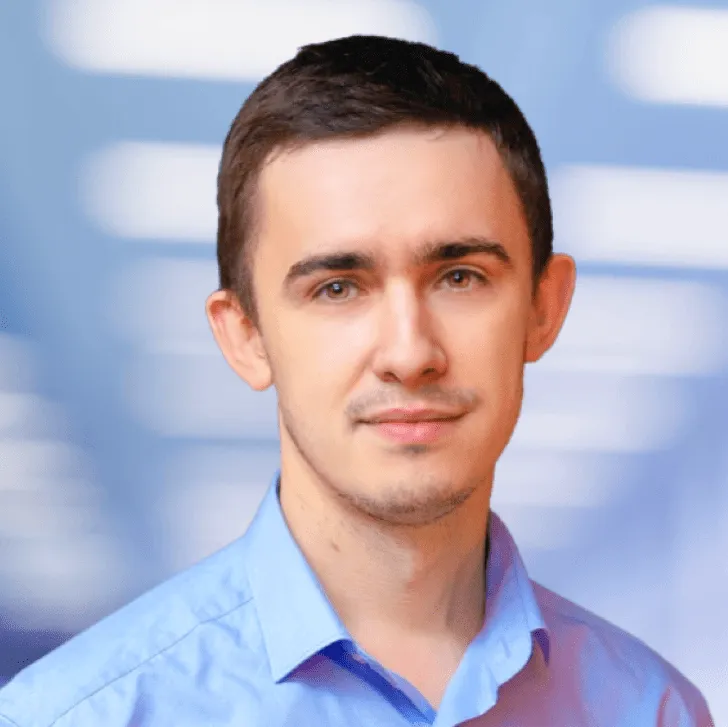
Evgeniy Altynpara is a CTO and member of the Forbes Councils’ community of tech professionals. He is an expert in software development and technological entrepreneurship and has 10+years of experience in digital transformation consulting in Healthcare, FinTech, Supply Chain and Logistics
Give us your impressions about this article
Give us your impressions about this article